Viewpoint: Making additive manufacturers smarter via the digital twin
by Alun WilliamsIn the last decade, an exciting dynamic is propelling manufacturing towards 3D printing, or additive manufacturing (AM), writes Bill Davis of Siemens Digital Industries Software, discussing the digital twin.
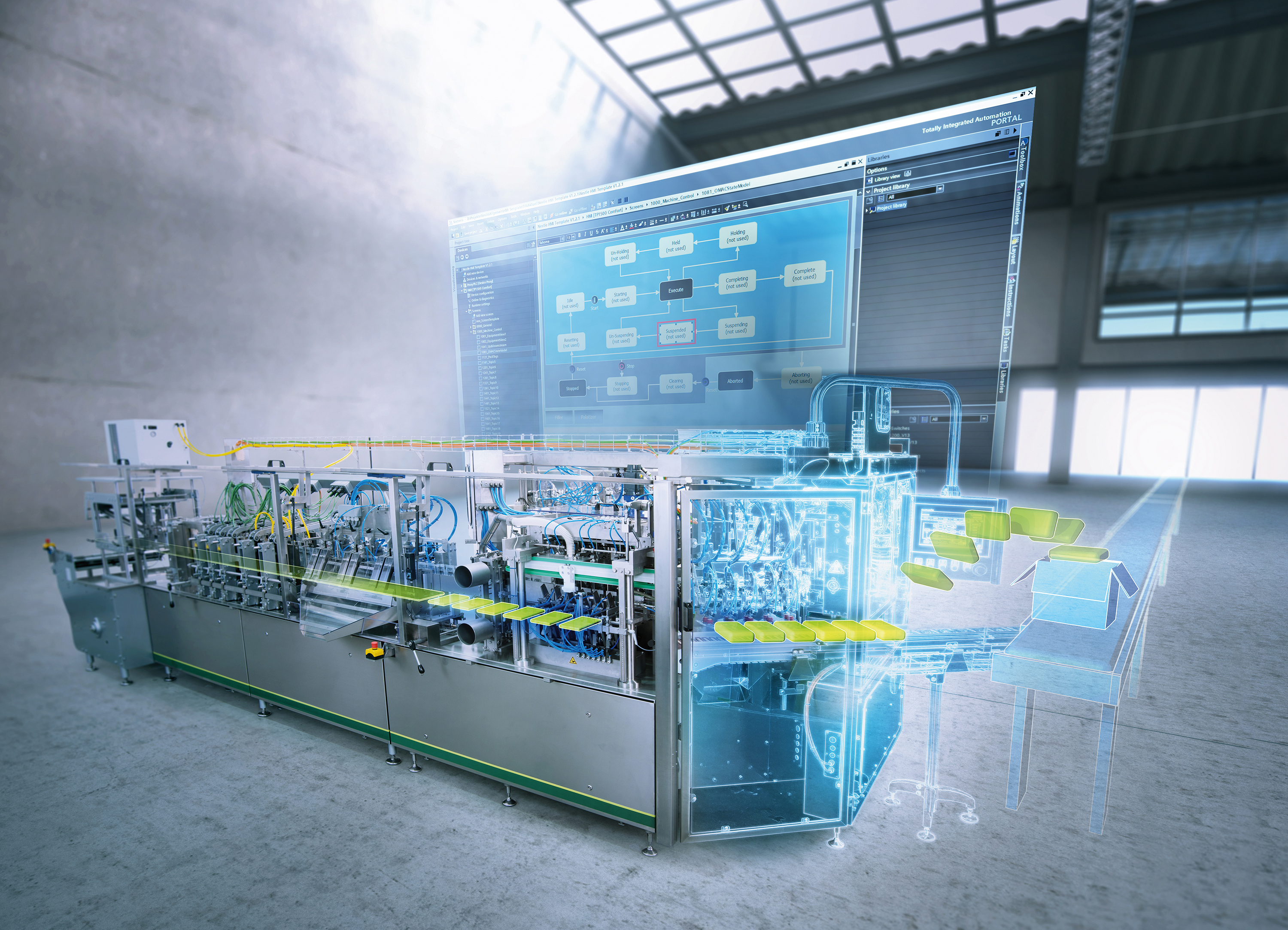
From a machining perspective, additive manufacturing enables designers to consolidate components, leading to less expensive parts, superior reliability, increased durability, and creative design.
Also, from a smart manufacturing perspective, a comprehensive digital twin is essential for successful additive manufacturing because it encompasses more than just the actual additive process. The digital twin includes post-process machining along with several make-ready processes for industrial machinery assembly. Moreover, the digital twin encompasses electrical, software, and PLC programming. It is a multi-disciplinary approach to create a truly comprehensive digital twin, and it is critical to have the right software to manage it.
The digital twin is a holistic representation of a product, its performance, and processes for manufacturing it. It corresponds to everything that constitutes today’s advanced devices: mechanical, electrical, hydraulic, and fluid, including pneumatics, design domains, performance, and simulation of the product. Many software packages can simulate each of these domains and perform them well. Unfortunately, the manufacturers producing and packaging consumer products with industrial machines must accommodate the changing requirements of customers. This environment requires a robust emphasis focusing on flexibility and abbreviated development times.
Digital twin process
The comprehensive digital twin is poised to address these challenges and optimize production beyond the factory floor. Therefore, this requires a digital twin, which represents all phases of the machine life, from ideation (engineering and simulation) and realization (manufacturing and requirements) through to utilization for operation and maintenance information. This abundance of information assists in completing the machine, including the individual serial, numbered parts.
The digital twin is crucial for building and executing the printing of additive parts while managing delivery, manufacturing, operations, and quality of manufacturing operations management. All these elements provide insight into coordinating the activities for delivering the correct parts at the right time. Manufacturing machinery requires elaborately coordinating the supply chain, internal manufacturing, and assembly. Thus, a united knowledge management piece is a vital component for designing and manufacturing.
Virtual machine simulation
Designing and manufacturing machines using a digital twin provides another advantage via the virtual machine simulation and commissioning process. This simulation refers to validating a manufacturing machine’s software code virtually before operating it physically on the factory floor.
Because the behavior of machines is driven by software, simulating the code on a virtual digital twin of the machine generates considerable benefits in reducing time and resources when commissioning a new manufacturing machine or reconfiguring a line to produce a new product type. With virtual commissioning, the PLC software code is validated in a controlled environment with a modular product development strategy. This process allows machine builders to perform the simulation upfront, linking the software to the modules.
Digital twin and safety
Then there is the physical safety aspect of virtual simulation. If the machine collides in the virtual world, it’s substantially safer and less expensive to resolve than with a physical machine. Virtual commissioning can drive the behaviors of the motors, as well as integrating that data into the kinematics. This methodology provides a powerful capability when a mechanism on a machine moves faster than expected, leading to an impact load higher than anticipated. Hence, replicating the kinematics in the virtual commissioning reveal hazards, resulting in providing swift resolutions.
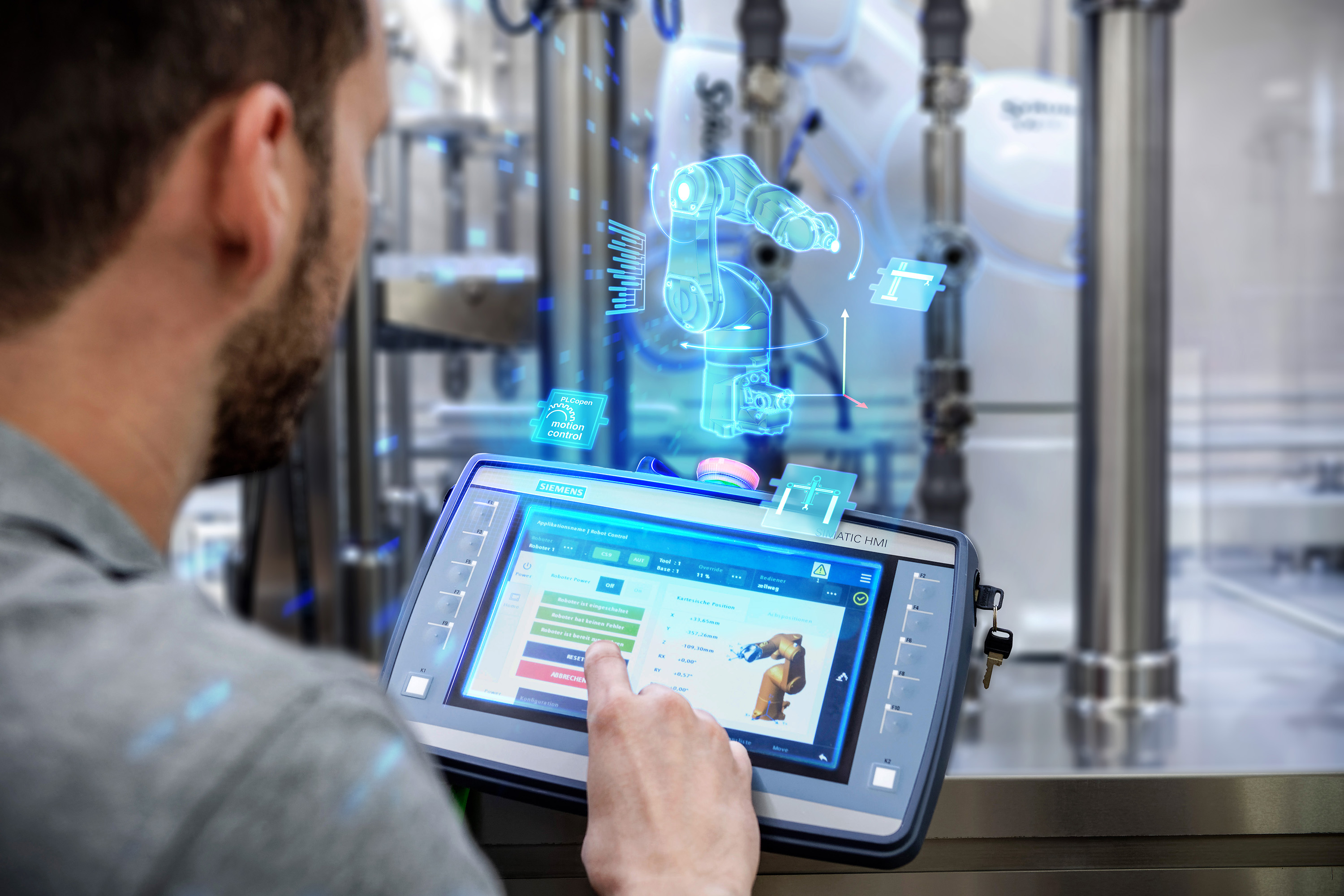
By embracing the digital twin and virtual commissioning, manufacturers can work closely with machine suppliers in a virtual environment, interacting with the machine digitally – paying significant dividends financially. No one wants to purchase a machine without seeing it operating correctly. Similarly, they will not buy it based strictly on the claim of simulating and validating the PLC code. A manufacturer must substantiate that a machine works correctly and efficiently in their environment before having it shipped to their factory. Thus, the virtual commissioning via the simulation process provides the necessary remedy for overcoming these verification hurdles. The resulting advantages exhibit positive results in many industries, including electronics.
Digital twin and electronics
Additive manufacturing is not the only industry positively impacted by adopting these innovative capabilities. For example, the digital twin and all the capabilities it enables is being embraced in the area of electronics manufacturing.
Manufacturers and machine builders are met with formidable challenges because electrical devices are entering the market rapidly. Therefore, separate lines for each product must be created and then taken apart, only to repeat this process in short production cycles. Hence, machine builders must deliver their new machines quickly, while rapidly adapting to short-term revisions.
Also, the commissioning phase of machines and lines is very dynamic from manual to automated production, saving a significant amount of time for meeting challenging time constraints of electronics companies. Siemens provides an ideal range of automation and digitalization solutions to create a digital twin of the machine. Therefore, it helps to develop new machines and lines quickly with significant flexibility.
Electronics companies need experts with a comprehensive portfolio for delivering a digital approach based on a digital twin, offering sophisticated hardware and software for small or large tasks with varying degrees of complexity. Thus, high-end applications are as simple to implement as rudimentary tasks, providing straightforward production processes where speed and cost-effectiveness are crucial. Consequently, industry trends and innovative advancements are changing the paradigm of manufacturing and machine suppliers.
Smart manufacturing
Therefore, smart manufacturing via a digital twin and virtual commissioning simulation is taking significant steps into the future of industrial mechanical design. This powerful feature, spanning design concept to product end-of-life, provides quality-of-life improvements to the design engineers and anyone in the business that controls manufacturing, operations, or management. Providing virtual commissioning capabilities empowers machine building, and a new process line, digitally simulating it before shipping the physical product, thus reducing downtime.
By using the Xcelerator portfolio, via Siemens Digital Industries Software suite of products, it assists to simulate testing virtually, saving time and money in modeling, and optimizing operations before construction or equipment installation begins. The digital twin for smart manufacturing saves time and money for the machine manufacturer, the product manufacturer, and the end customer. They now know what needs to be built, thus providing exceptional value for all parties. Smart manufacturing with a comprehensive digital twin is where today meets tomorrow.
Author
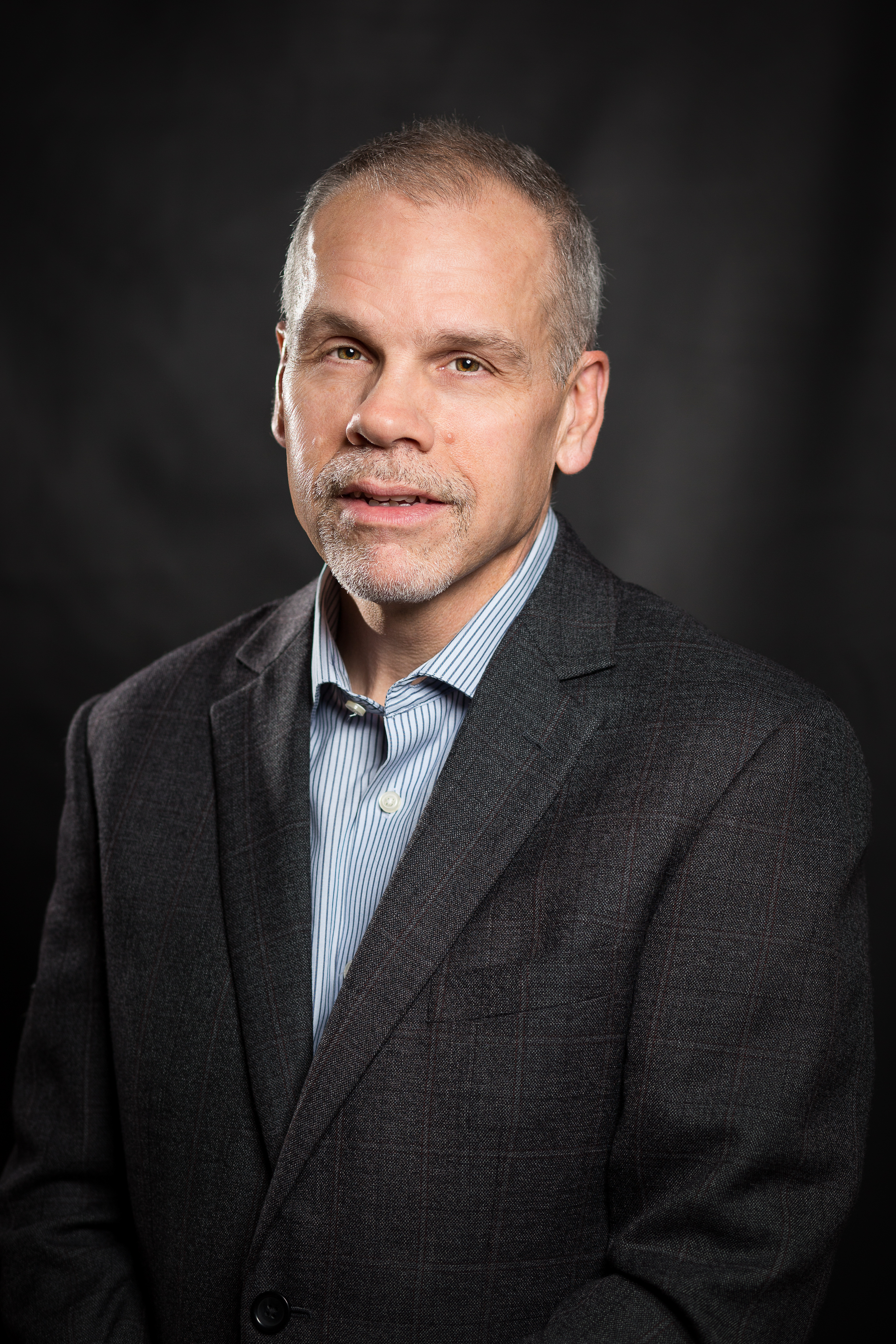
Bill Davis is the Solution Director of Industrial Machinery and Heavy Equipment Industry for Siemens Digital Industries Software. His experience and insights have been acquired from a career spanning 30 years in engineering and operations management with machinery and heavy equipment companies. Bill holds a master’s degree in Business Administration from Marquette University, with a concentration in Operations Management and Strategic Marketing, as well as a Bachelor of Science degree in Mechanical Engineering from Milwaukee School of Engineering.