How battery calorimetry can enhance the lifetime and safety of Lithium-ion and post-Li cells
by Steph HazlegreavesDr Carlos Ziebert, head of IAM-AWP’s Calorimeter Center, KIT, explains how battery calorimetry can enhance the lifetime and safety of Lithium-ion and post-Li cells
Established in 2011, the IAM-AWP Calorimeter Center currently operates Europe’s largest Battery Calorimeter Laboratory. It provides six Accelerating Rate Calorimeters (ARCs) of different sizes – from coin to large pouch or prismatic automotive format – which allow the evaluation of thermodynamic, thermal and safety data for Lithium-ion and post-Li cells on material, cell and pack level under quasiadiabatic and isoperibolic environments for both normal and abuse conditions (thermal, electrical, mechanical). These data can be used on all levels of the value chain – from the safe materials design up to the optimisation of the thermal management and the safety systems.
On the materials level, differential scanning calorimeters (DSC), laser flash analysers (LFA) and an extremely sensible Setaram C80 Tian-Calvet calorimeter (s. Fig.1 left side) provide thermodynamic parameters, such as heat capacity, thermal conductivity or formation enthalpy on the materials level. In the larger Setaram MS80 Tian-Calvet calorimeter (s. Fig.1 right side), cylindrical cells up to 21700 format fit in and their heat generation during cycling can be determined with great accuracy by direct heat flow measurement. The heat flow is determined by the 3D Tian-Calvet Sensor arrangement, where both the sample and the reference vessel are surrounded by rings with hundreds of thermocouples (s. Fig. 1 centre).
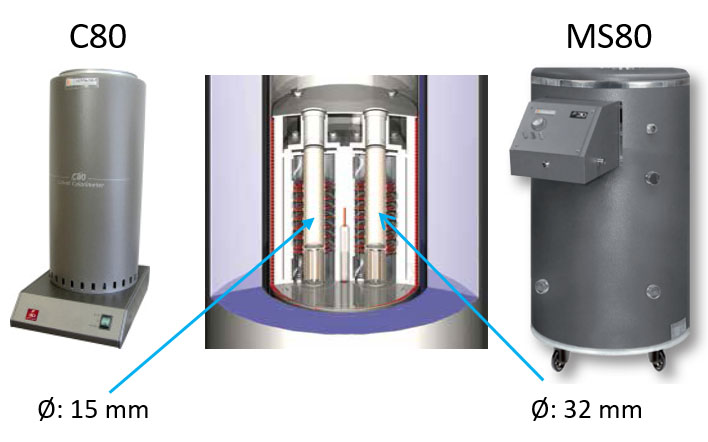
Post-Li cells
These studies are especially important for Post-Li cells, which make use of more abundant materials, such as sodium or magnesium instead of Li, Ni and Co. These materials are in the focus of the POLiS (Post Lithium Storage) Cluster of Excellence, that was acquired in late 2018 jointly by KIT and Ulm university within the highly competitive Excellence Strategy competition of the federation and the federal states. It has a budget of about €7 million per year and is scheduled for seven years. In this cluster, the IAM-AWP Calorimeter Center is responsible for thermal characterisation and safety testing. Both have to be started, now on the smaller scale level and need to be continued to ensure that the cells can be safely up-scaled.
Current Li-ion cells
It is clear that safety issues have a major influence on consumers’ willingness to adopt the current Li-ion battery technology, because an uncontrollable temperature increase (so-called thermal runaway) can cause an ignition or even explosion of the battery with the simultaneous release of toxic gases. Thus, thermal management and safety are of utmost importance for the electrification of transport and stationary storage. The six robust Accelerating Rate Calorimeters (ARCs, Thermal Hazard Technology) can bring advancements in the thermal management, cycle life and safety of batteries.
For studies on heat generation and dissipation during charging and discharging, they are coupled to battery cyclers. Isoperibolic (constant temperature of the calorimeter) or quasiadiabatic (no heat exchange with the calorimeter) ambient conditions are adjusted by heaters and thermocouples that are located in the lid, bottom and side walls of the calorimeter chamber, in which the cell is inserted (s. Figure 2). For application in the thermal management system, the measured temperature data are converted into generated and dissipated heat data by determination of specific heat capacity and heat transfer coefficient.
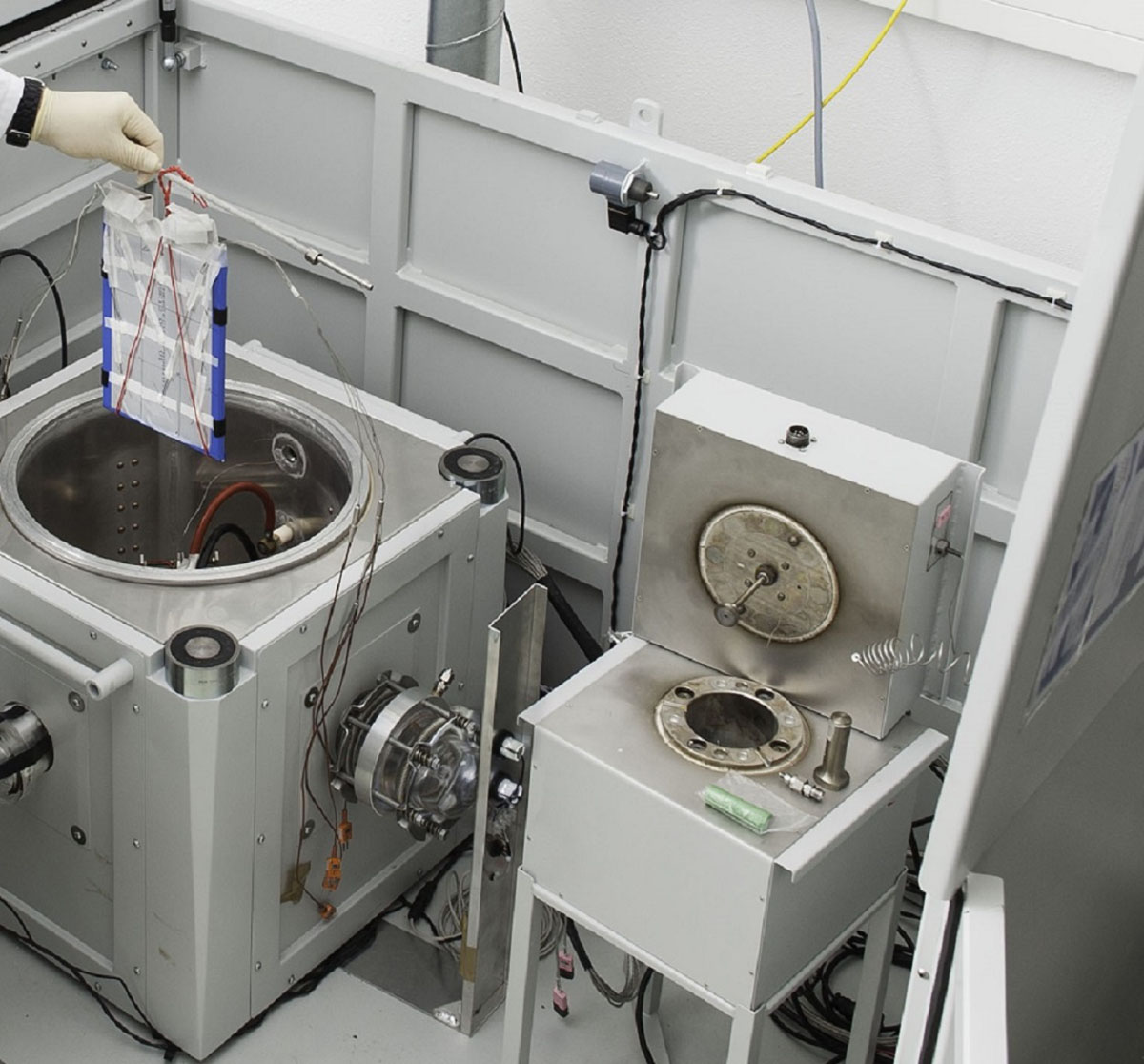
The cycle life can be studied by performing calendaric and cyclic ageing tests and characterising the cells at fixed time intervals concerning changes in heat generation and temperature profile, which serves as a “fingerprint” for the state-of-health (SOH). Once the cells have reached their termination criterion, the reversible and the irreversible heat are measured using entropy measurement and electrochemical impedance spectroscopy (EIS). These data can be used for the parameterization of impedance-based electrical equivalent circuit models (EECMs) and ageing models. In addition, some cells are analysed post-mortem, i.e. disassembled in an inert gas atmosphere and the changes in the chemical composition, the morphology and the structure of the electrodes are determined.
Moreover, the safety of fresh cells and the influence of ageing on the hazard potential can be quantitatively determined by performing the following three types of safety tests in the ARCs:
- Electrical abuse: External/internal short circuit test, overcharge test, over-discharge test.
- Mechanical abuse: Nail test.
- Thermal abuse: Heat-Wait-Seek test, ramp heating test, thermal propagation test.
Self-heating, thermal stability and thermal runaway are characterised and the critical parameters and their thresholds for safe cell operation are determined. Another important issue concerns the venting gases, which can be collected during the abuse tests and analysed ex-situ. Gas chromatography (GC) method with two detectors (mass spectrometry (MS) and thermal conductivity detector (TCD)) are available to detect and quantify the gases. Knowledge of the gas composition under the various cell abuse scenarios reveals the relevant decomposition paths and gives an idea, which protective measures are necessary, for example, to delay or prevent the cell fire caused by the ignition of vent gases or thermal runaway.
To summarise, battery calorimetry provides quantitative and system relevant data for temperature, heat and pressure development of materials and cells as fast feedback for cell development and as input data for simulations.
Please note: This is a commercial profile
Contributor Profile
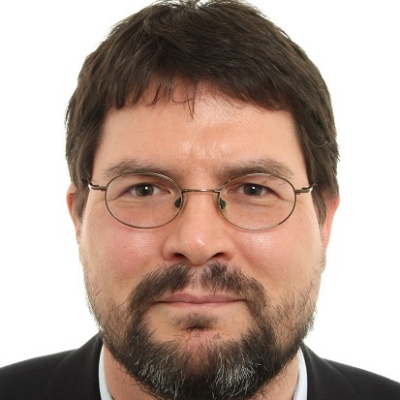
Carlos Ziebert
Head of the Calorimeter Center
Karlsruhe Institute of Technology (KIT)
Phone: +49 721/608 22919
Email: carlos.ziebert@kit.edu
Website: Visit Website