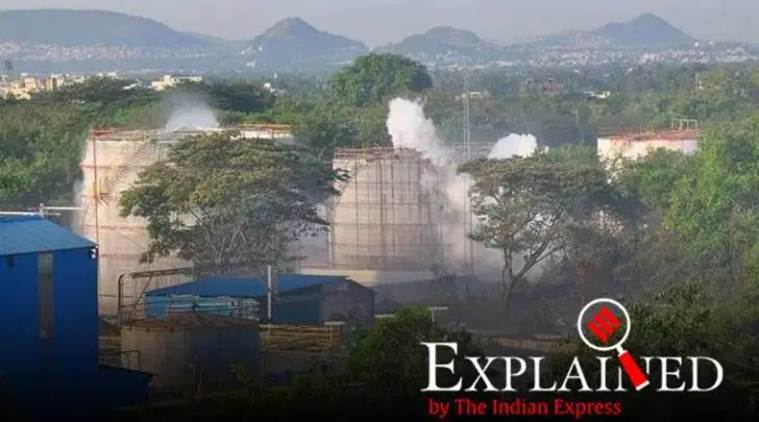
The Indian Express
An Expert Explains: What can go wrong with styrene?
On May 7, a leak of styrene gas in Visakhapatnam left 11 dead and affected thousands. A leading scientist discusses the compound, health implications, and possible causes for the leak, based on what is known.
by Amitabh SinhaOn May 7, a leak of styrene gas in Visakhapatnam left 11 dead and affected thousands. A leading scientist, Dr Swaminathan Sivaram, former director of National Chemical Laboratory in Pune, spoke to The Indian Express on the compound, health implications, and possible causes for the leak, based on what is known.
Based on what we know, what could have happened in Vizag on May 7?
Let me first summarise what we do know. The plant was under start-up after a lockdown of 40 days. The tank that leaked had a capacity of 2,400 tonnes, with 1,800 tonnes of styrene present at the time. The operators were checking the storage tank, and it has been reported that one of the valves in the tank was probably not handled well. It also appears that there was a technical glitch in the refrigerator unit of the tank. From videos and photos taken immediately after the accident, copious amounts of white dense vapours are seen gushing from somewhere at the bottom of the tank.
Now, a bit about styrene. It is actually a colourless liquid, and not a gas. Styrene exists as a single molecule, but is unstable and has a high propensity for auto-polymerisation, meaning it tries to combine with itself to make long chains, especially at temperatures over 65°C. This process is exothermic, that is, a lot of heat is released during auto-polymerisation, and can become uncontrollable.
For these reasons, styrene is always stored at relatively low temperatures (between 15°C and 20°C). This is to avoid inadvertent polymerisation and the resultant generation of heat. A small amount of another chemical — called an inhibitor — such as para-tertiary-butyl-catechol is also added to stored styrene in order to prevent polymerisation. Despite these precautions, in geographies or seasons that have significant temperature differences between night and day, small amounts of styrene vaporise when the temperature is high, and then condenses on tank roofs, walls, or fittings, when it cools down. The inhibitor exists only in the liquid phase, and thus styrene vapours don’t have the inhibitor mixed in them. So, in condensed styrene stuck on walls, roof or fittings, there is nothing to prevent auto-polymerisation. This often leads to a plugging of pressure relief valves in the tank or in the pipelines.
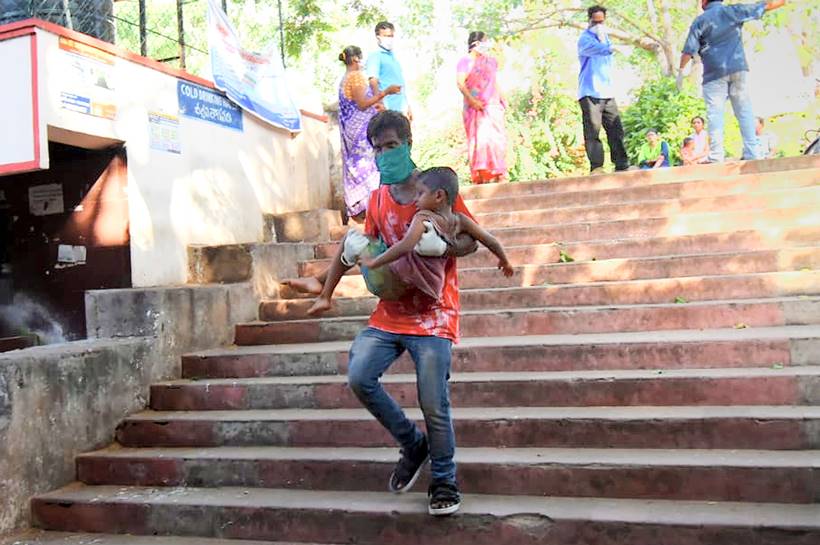
Now based on all this information, here is what I think could have happened in Vizag: Due to the long shutdown, it is possible that slow polymerisation of styrene in the tank had begun, especially where it might have been in condensed state. This probably went unnoticed. In addition, there have been reports that some valves had failed to function at the time of start-up, probably because of choking, and it is quite possible that the process adopted for declogging these valves might have resulted in them giving way, and the liquid styrene leaking out. As the liquid streamed out of the small orifice, it would have led to a sudden turbulence and mixing in the tank, which in turn could have led to violent polymerisation. This probably resulted in an increase in temperature inside the tank, facilitating the vaporisation of styrene, and these vapours escaping. And because the refrigeration system had also malfunctioned, there was nothing to control the rise of temperature inside the tank.
An alternative hypothesis is that styrene condensate formed on the roof and walls of the tank might have fallen into the liquid, and could have become the reason for initiation of polymerisation.
Now, the fact that long storage, lack of refrigeration, or depleting inhibitor content leads to slow polymerisation is not unknown. It happens occasionally, and is detected during routine monitoring of the storage tank. If timely intervention is not made, it could lead to a runaway explosive condition. I do not think that kind of explosive condition existed in the Vizag tanks at the time of the accident. Otherwise, the result could have been far more catastrophic, as the tank itself could have ruptured.
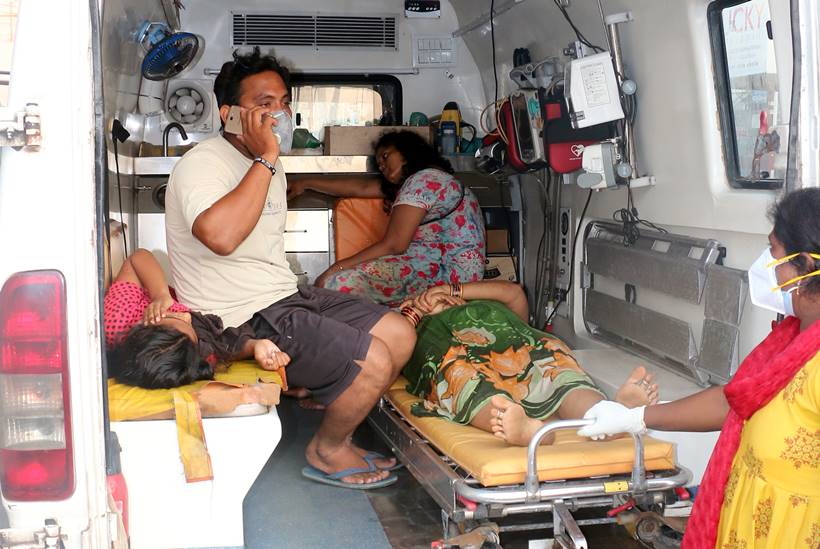
The accident revived memories of Bhopal. As someone who handled the aftermath of the Bhopal leak, do you see parallels?
I think it is unfair to compare this accident with the leak of methyl isocyanate (MIC) in Bhopal. MIC is far more poisonous and toxic. The concentration of MIC that is classified as immediately dangerous to life and health (IDLH) is just 2-5 parts per million, whereas for styrene, this is 700 ppm. MIC’s biological response in human beings is similar to that of hydrogen cyanide. It blocks the functions of haemoglobin in the blood.
The only thing for which I can speak of both in the same breath is that both accidents were avoidable with a little extra care.
Does this suggest an element of negligence in the Vizag accident?
All accidents have an inherent element of negligence. It is often said that an accident is a consequence of confluence of 95% unsafe acts and 5% unsafe conditions. Several standard precautions seem to have been missed. A standard practice is to analyse the contents of the storage tanks daily for oxygen, inhibitor and polymer concentrations. The temperature inside the tank also needs to be monitored regularly, and kept as low as possible, with continuous refrigeration. These checks are even more important during long plant shutdowns.
Inadvertent polymerisation of styrene gives us enough notice and warnings, as temperature rises very slowly. Even in the absence of an inhibitor, it takes about 25 days for the temperature in the tank to increase from 20°C to 30°C. So periodic monitoring is all that is required to ensure safety.
Industry has been handling styrene for decades now. There is no documented record of a major styrene-related accident anywhere in the world. Some minor accidents involving rail car containers and road tankers have been reported. One of the biggest incidents reported was an explosion in a shipping tanker in a South Korean port last year. This is true of the industry in India as well. India imports close to 1.5mn tonnes of styrene annually and processes it into several products we use daily.
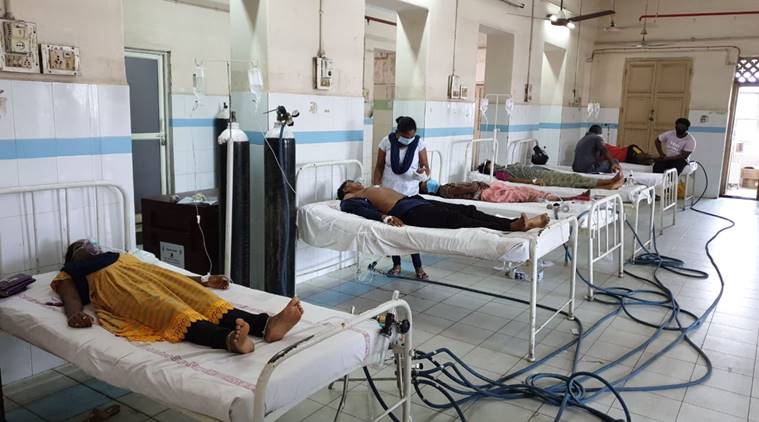
What does styrene do to the body?
Styrene has low oral toxicity and moderate inhalation toxicity. Styrene vapours are an irritant to eyes, gastro-intestinal tract, mucous membranes, and respiratory tract. But long-term health effects of styrene are very small. There is no evidence that it induces any kind of cancer. Most of the symptoms of exposure to styrene are reversible.
What does the Vizag accident say about industrial safety standards in India?
In recent years the record of process safety in the chemical industry has significantly improved, thanks to technology, automation and IT. India has some unique problems that we need to address quickly. A lot of our chemical manufacturing is in the small and medium sectors, whose ability to invest in industrial and environmental safety as well as occupational health is limited. Several of our manufacturing plants are ageing and reluctant to invest in capital either to revamp or scrap/rebuild, and that is a matter of concern. Urban populations have encroached on spaces that were originally demarcated for industry, including the buffer (and green) zones that all chemical industry was mandated to follow. There is also an increasing tendency to skip long-term training and skill development by resorting to casual labour in the operational area. The chemical industry will face severe shortage of skilled operating personnel in the years to come.