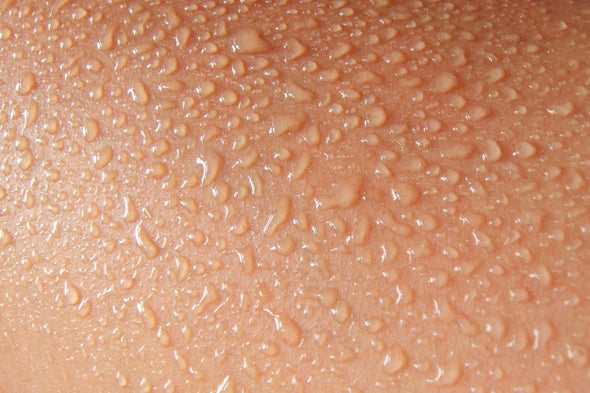
Sweating Robot Beats the Heat
By leaking water, a soft robotic gripper cools itself more efficiently than humans do
by Sophie BushwickElectronics cannot handle the heat. That is why computers rely on fans, and car engines need radiators. But these cooling devices are necessarily rigid, which makes them a bad fit for soft robots made from stretchy, flexible plastics instead of metal. So some Cornell University researchers have taken their inspiration from perspiration and developed a soft robotic gripper that automatically starts sweating when temperatures rise.
Thanks to their squishy construction, soft robots are sometimes more adaptable and durable—and can be less likely to cause injury—than their metallic counterparts. Yet these machines’ flexible materials can also make them vulnerable to high temperatures. The polymers used in many soft robots hold heat longer than metals do, and their stiffness changes when the temperature is altered. These properties can affect the way the robots bend and thus their ability to grasp objects. Giving them the old-fashioned trait of sweating may help.
“I think it’s a really great idea,” says Cecilia Laschi, a soft robotics expert at the the BioRobotics Institute at the Sant’Anna School of Advances Studies in Italy, who was not involved in the new study. “One of the main contributions of this field is really to make us imagine this kind of robot with lifelike abilities, something that was not possible before, with traditional robotics technology.”
Sweating is not just lifelike; it is also an extremely efficient cooling method. “Elite marathon runners in the right conditions have been known to lose almost four liters of sweat an hour,” said study co-author Thomas Wallin, a Ph.D. candidate at Cornell at the time of the research and now a materials scientist at Facebook Reality Labs, at a recent press conference. “This corresponds to roughly 2.5 kilowatts of cooling capacity.” For comparison, he added, a home refrigerator consumes about one kilowatt of energy over the course of an hour.
The researchers suggest this technique is particularly suited to soft robots. To move and interact with their surroundings, many of these devices use hydraulic systems to pump water into a balloonlike “finger”—usually made from materials such as hydrogel, a water-rich polymer—to make it inflate and bend in a predictable way. Adding pores to the gripper finger would allow it to release some of its water as sweat. But the liquid would have to leak out in a controlled fashion, or the gripper would deflate too quickly.
To control this process, the Cornell team built their three-pronged gripper robot from “smart gels” that change in size when the temperature increases. The researchers were also able to use multiple materials to build each hollow finger by selecting ones that could be 3-D printed in a process called multimaterial stereolithography. For the bulk of the finger structure itself, Wallin and his colleagues used a polymer called PNIPA, which starts shrinking when temperatures hit about 40 degrees Celsius. And for the outward-facing side, they turned to a chemical called acrylamide, which expands at high temperatures. They gave this part of the finger a texture designed to encourage evaporation and perforated it with tiny pores a fifth of a millimeter wide. As the fingers heat up, their volume shrinks, and the pores expand, squeezing the liquid contents out through the holes.
“The best part of this synthetic strategy is that the thermal regulatory performance is based in the material itself,” Wallin said at the press event. “We did not need to add sensors or other components to control the sweating rate. When the local temperature rose above the transition, the pores would simply open and close on their own.”
He and his colleagues also designed a nonsweating version of the gripper, which acted as a control device. To compare the robots’ abilities to shed heat, they used both machines to pick up hot objects while a fan blew air over them. The sweating gripper dropped its temperature six times faster than the dry one, cooling itself at a rate of 107 watts per kilogram of weight—three times greater than the temperature-regulating efficiency of a sweating animal, according to the researchers. The study was published this week in Science Robotics.
Credit: From “Autonomic Perspiration in 3D-Printed Hydrogel Actuators,” by Anand K. Mishra et al., in Science Robotics, Vol. 5, No. 38; January 29, 2020
The concept does have some kinks to iron out. For one thing, the same water reservoir that feeds the sweating pores also provides the finger’s ability to bend. This arrangement means that as liquid drips out of the finger, the control system must modify the pressure in the device to make up for the lost volume. The team found, however, that the fingers could still bend at the required angles even with less water in reserve. Another issue is the fact that grippers lose some of their friction when covered with slippery water. The researchers suggest that future versions might be made of a material that wrinkles when wet—like human fingers do—increasing the ability to grip. Ultimately, the current prototype is a proof of concept: it demonstrates that perspiration is a viable cooling method for soft robots and gives scientists a platform they can continue to modify and improve.
Beyond gripping, Laschi notes, soft robots have a wide variety of potential applications. “One of them is the biomedical field, because you can apply soft robots in surgery, rehabilitation and assistance to people,” she says. Because they are more compatible with fragile human bodies, Laschi adds, these types of robots are good in situations in which a machine must make direct contact with a person. Researchers are also looking into soft robots that can explore and monitor new environments. Many of these machines use water or other liquids to move their components, and the Cornell researchers’ new sweating method might work well with some of them. “Fluidic actuation is very popular in soft robotics, so there are so many cases where their idea and their solution can be applied,” Laschi says. “In this sense, I think it’s very powerful.”